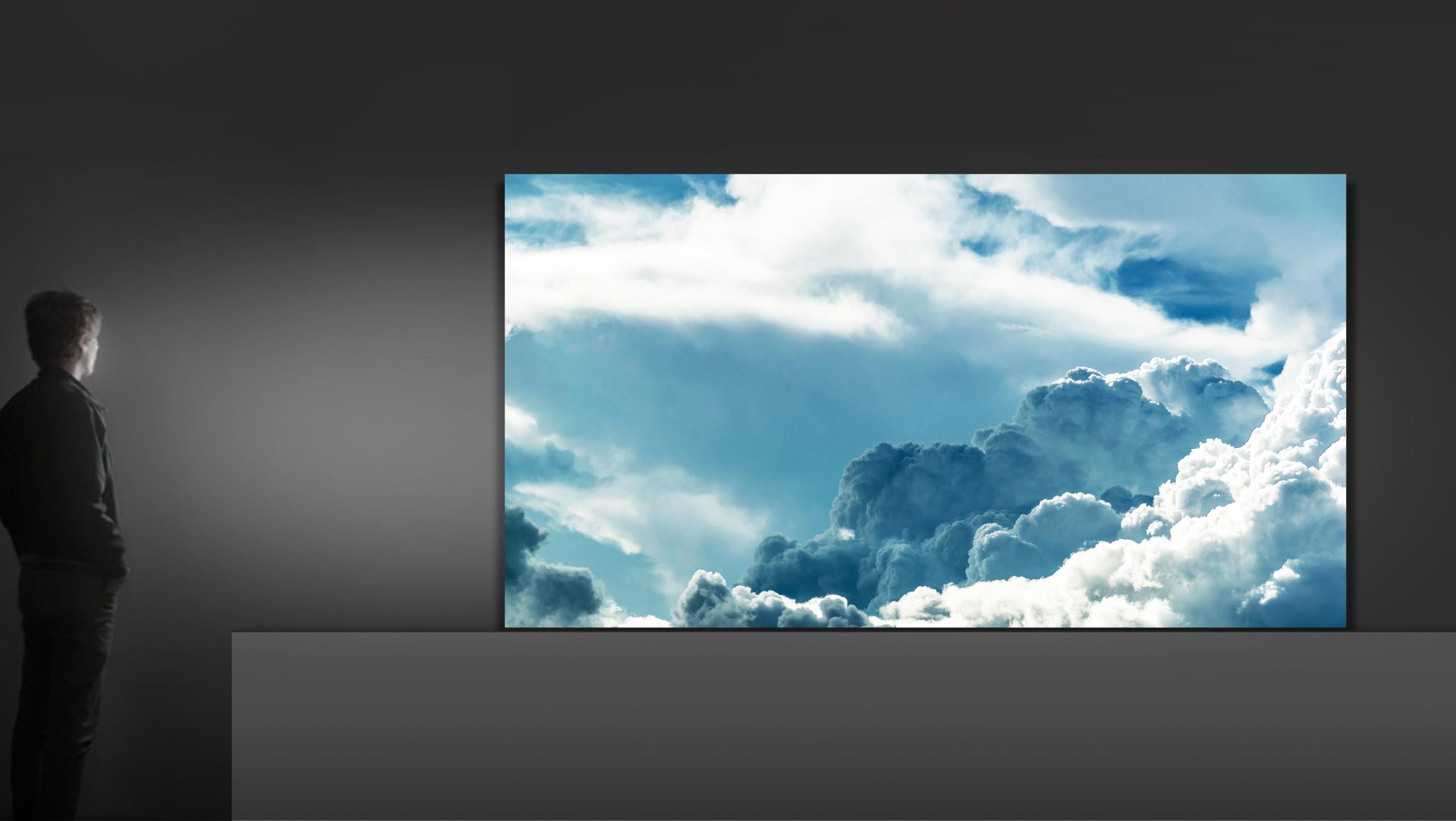
Display Week: DSCC’s Analysis Suggest MicroLED A Niche Product; Manufacturing Challenges Remain
May 17, 2021 by Dave Haynes
MicroLED has received a ton of buzz in digital signage circles the last 2-3 years because of the proposition of building big seamless video walls that look as good as LCD or OLED.
The big barrier to widespread adoption has been cost – driven in part by a need to make production more efficient and speedy, while also minimizing production flaws.
The terms that comes up a lot are mass transfer and yield.
Mass transfer has to do with finding production processes that will shift a LOT of teeny LED light emitters at once and place them hyper-accurately on the display surface. Existing mainstream methods for picking and placing LED light chips are just too slow for microLED because of the sheer number of chips needed to make a big display, even though a lay person looking at the manufacturing machines would think the machines are placing chips at dizzyingly fast pace.
Instead of single lights, mass transfer means shifting and placing many at once, which speeds things up and reduces production costs.
Various manufacturers are touting processes that use fluids, magnets, stamping and even printing to lay down the LED chips in mass quantities.
The other issue is manufacturing yield, the term that roughly describes production accuracy and efficiency. In simple terms, if you manufacture stuff, when you make 1,000 units, you hope 1,000 units are perfect. But there may be one or more flawed units, so that drops the yield into the 99 percentile.
An analyst at Display Supply Chain’s annual business conference today at Display Week had an interesting slide about yield in his presentation on microLED, breaking down how even a seemingly great level of production efficiency means a lot of flaws when you are talking about a microLED video wall.
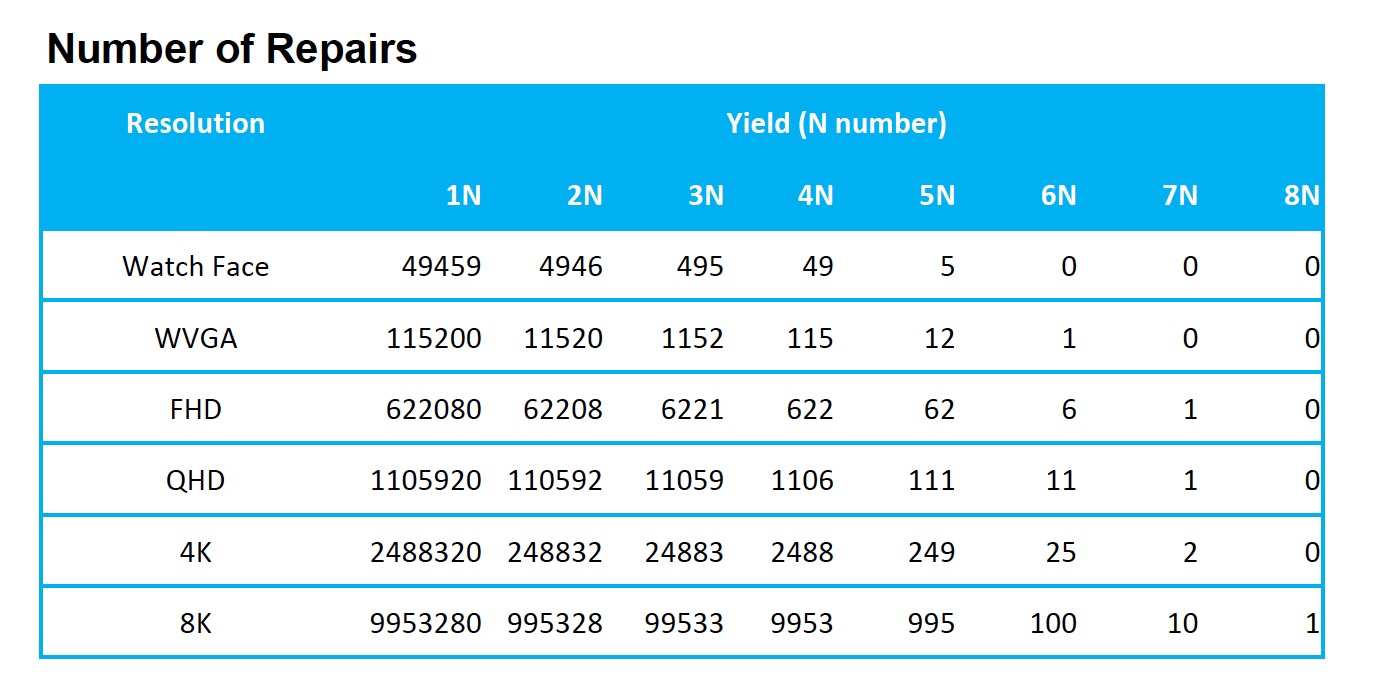
The common measure is in terms of nines, as in 99.999% yield being five nines. That would seem like an impressive level of accuracy, but DSCC suggests if that was for a microLED video wall with 4K resolution, that would mean almost 2,500 dead or flawed microLED light emitters to repair or compensate for in some way.
Repairs take time and money, so one of the other ideas out there is to have redundant microLED lights, so that flawed lights would be covered off by neighboring lights. But more lights means more cost and complexity.
DSCC also gets into, into its microLED outlook, some ideas around reducing hardware costs.
It notes a Korean manufacturer, Seoul Viosys, is touting a “triad” chip that puts the three red, green and blue sub-pixels (LED lights) on the same chip, which means the amount of chips being mass transferred would be reduced by two-thirds.
DSCC also cited the North Carolina start-up X Display, which is touting technology that marries the RGB microLED light emitters with the integrated circuit, which removes the need for the thin film transistor backplane (more simply, the plate the LED chips normally get bonded to).
DSCC sums up the business prospects for microLED like this:
- MicroLED is grabbing headlines but MiniLED LCD is the technology ready for mass production.
- Revenues for MicroLED displays is expected to reach $2.8B by 2026.
- TV will be the largest segment, due to the high price (over $15k per unit).
- Further cost reductions will be required to compete against other advanced TV technologies (OLED, QDLCD, MiniLED LCD).
- We (DSCC) expect that MicroLED will not be competitive in Smartphones, Tablets and Notebooks.
Leave a comment